IBS Coated Silicon Carbide Optics
Silicon carbide (SiC) is emerging as a leading optical substrate for high-performance applications in the space, defense, and semiconductor sectors. Known for its outstanding thermal and mechanical properties, SiC provides a stable platform for optics operating under extreme environmental conditions.
SiC is a non-toxic material, and it can be formed into almost any desired shape. It has low density, a low coefficient of thermal expansion, and excellent thermal stability, and it also has high specific stiffness and some important resonant frequency advantages. It can transmit heat a hundred times faster than glass and exhibits more than four times the resistance to gravity deformation.
OPTOMAN has applied Ion Beam Sputtering coating technology to coat high-quality SiC substrates and offers customizable and application-oriented solutions.
TECHNICAL CAPABILITIES
- Highly customized and application-optimized solutions
- High LIDT coatings with high surface flatness control
- OPTOMAN understands the importance of repeatability, has many metrology processes, and ensures that every optics act as promised
- IBS Coatings spectral range: 193–5000 nm
- Reflectivity: 99.9%
- Available Size: 3–420 mm
- Flatness: Up to < λ/20
- Surface Quality: Up to 10-5 S-D over CA (MIL-PRF-13830B)
WHY CHOOSE SILICON CARBIDE FOR OPTICS
SiC is a non-toxic, machinable ceramic that offers several performance advantages:
- Low density – Reduces system weight
- High stiffness and strength – Maintains precision shape under stress
- Low coefficient of thermal expansion – Ensures dimensional stability
- Excellent thermal conductivity – Transmits heat up to 100x faster than glass
- High resistance to gravity-induced deformation – 4x better than glass
SiC comes in nearly 250 crystalline forms, with characteristics such as strength, density, and stress behavior shaped by the manufacturing method. Different types of SiC, like reaction bonded, sintered, and CVD SiC offer distinct performance profiles and levels of production complexity. Selecting the right type is essential, properly manufactured SiC can greatly enhance optical applications, while poor quality can be detrimental.
- Reaction bonded SiC (RB-SIC)
- Sintered SiC
- 3D Printed SiC
- Hot press sintered SiC
- Reaction sintered SiC
- CVD SiC
- Converted SiC
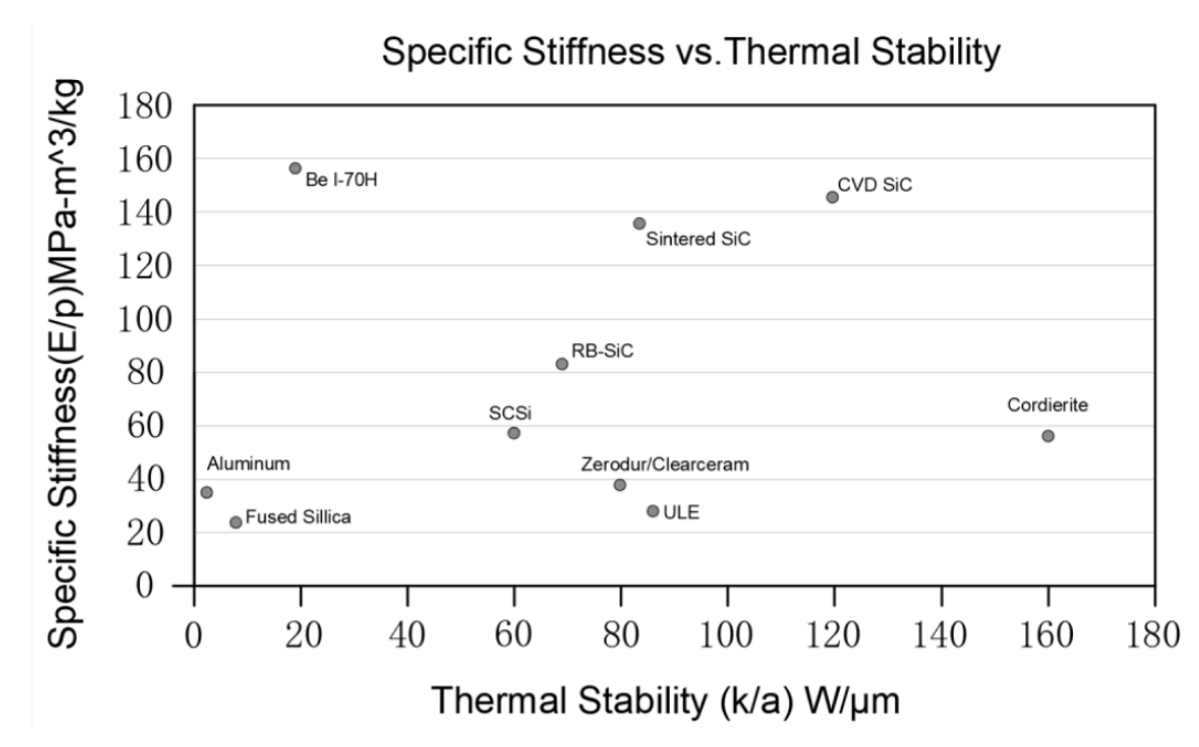
DESIGN EXAMPLE
Substrate material: SiC (CVD grade)
Coatings (IBS):
HRp>99.7% @ 760 nm – 860 nm, AOI=45°
GDD Rp<60 fs² @ 770–845 nm
LIDT: >0.2 J/cm², 800 nm, 35 fs, 10 Hz
LIDT measurement performed at Lidaris
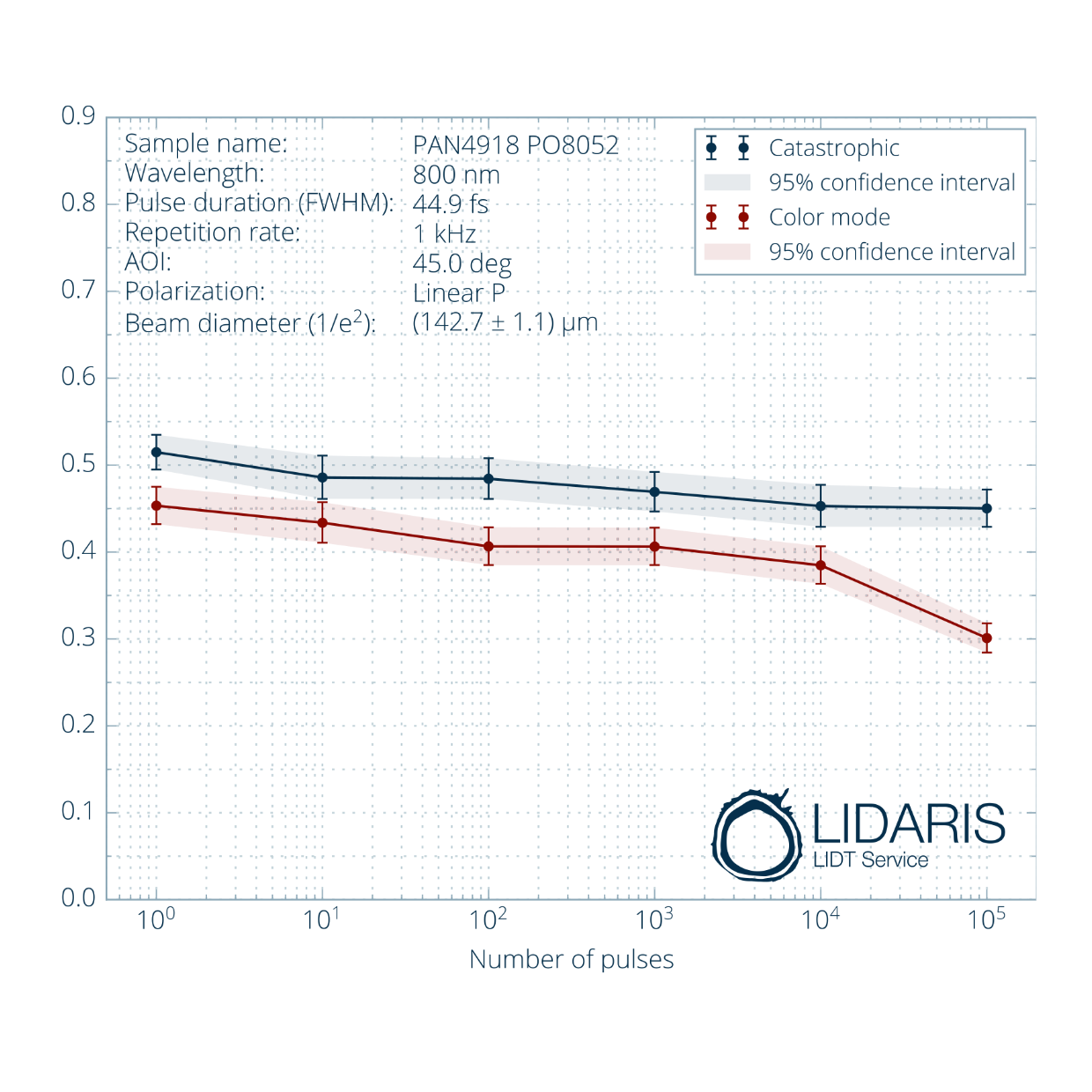
Reflectivity Rp measurement at 45° AOI
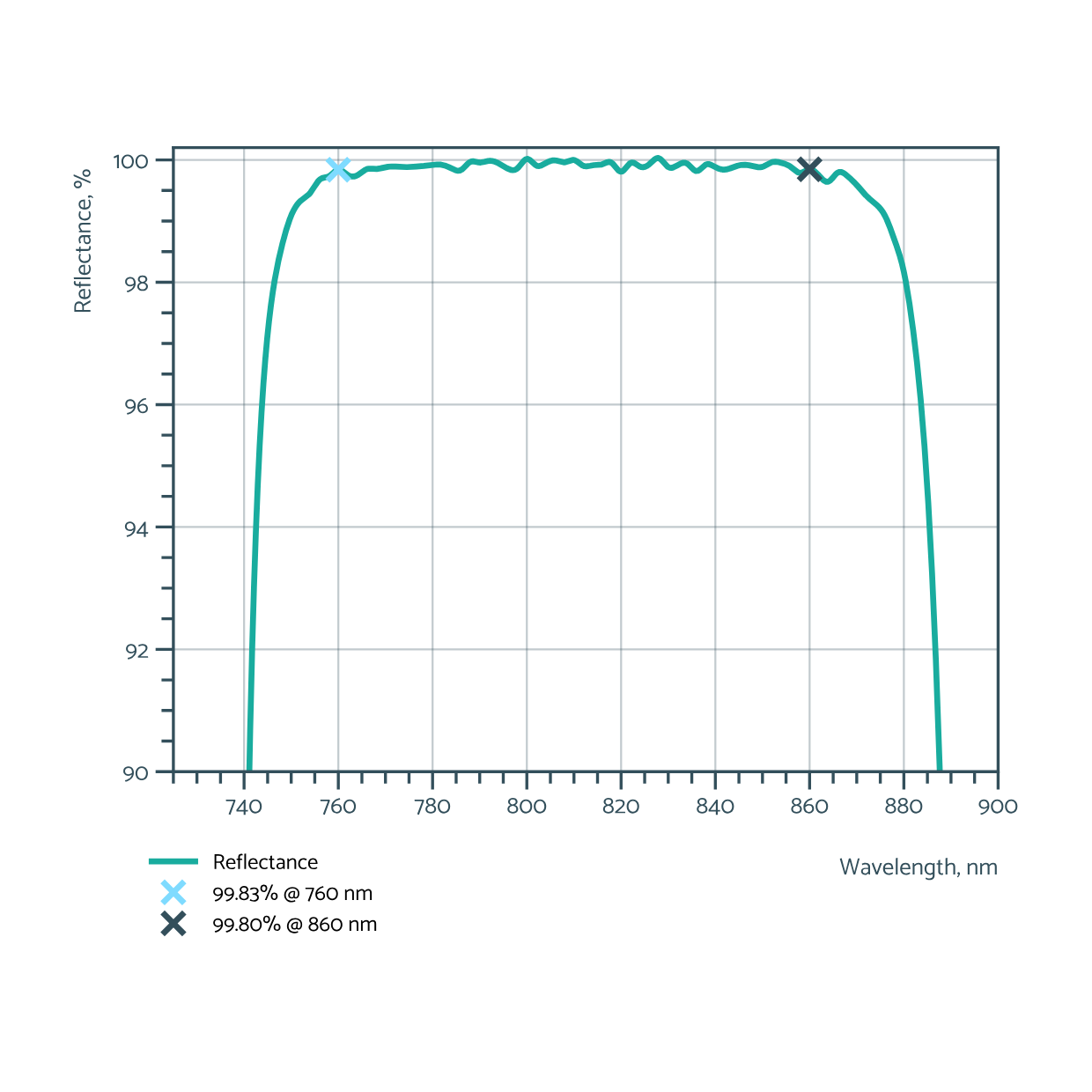
LOW ROUGHNESS
OPTOMAN IBS HR coating on average adds 2Å of root-mean-square (RMS) roughness according to atomic force microscope (AFM) measurements.
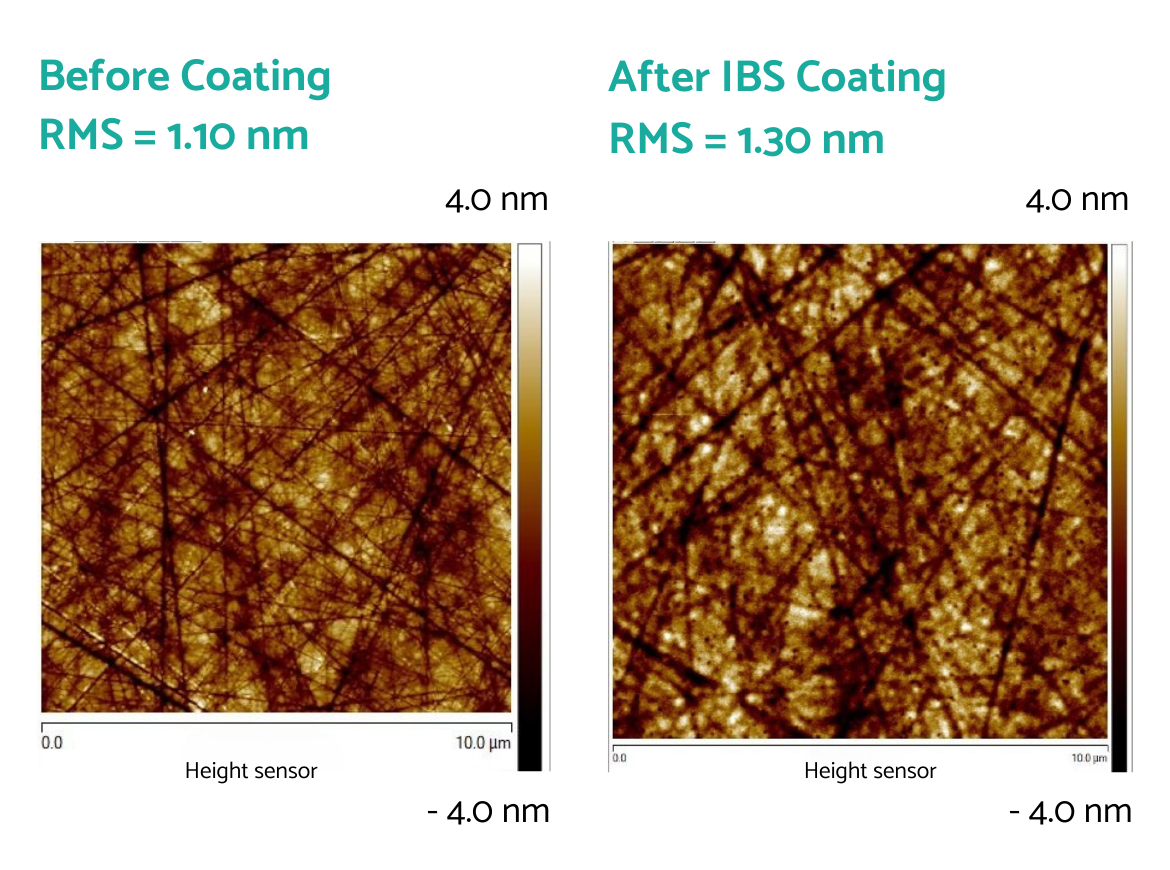
ABRASION TESTS
Abrasion resistance testing is specified when coatings will be exposed to the environment and regular cleaning/handling on the completed optical component. The test simulates real-world wear and provides information about the mechanical resistance of optics.
OPTOMAN IBS-coated SiC optics comply with the highest degree of severity according to the abrasion test.
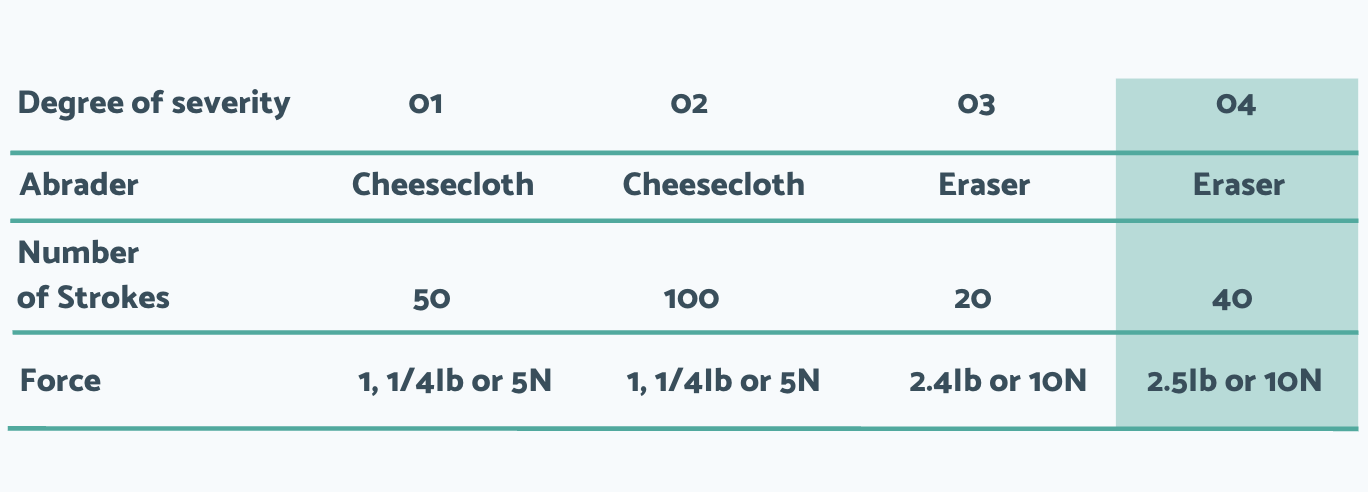