Laser Optics for Surgical Applications
Surgeries have come a long way since lasers were invented. Using lasers in surgeries offers several advantages over traditional surgical methods, including extreme precision, minimal damage to surrounding tissue, faster recovery times, etc.
Lasers have been implemented in many kinds of operations, such as kidney stone removal, prostate surgeries, laser angioplasty, dental treatments, vascular lesion treatments, and much more. The versatility comes from applying various types of lasers, each with wavelengths that correspond to different absorption bands in human body tissues.
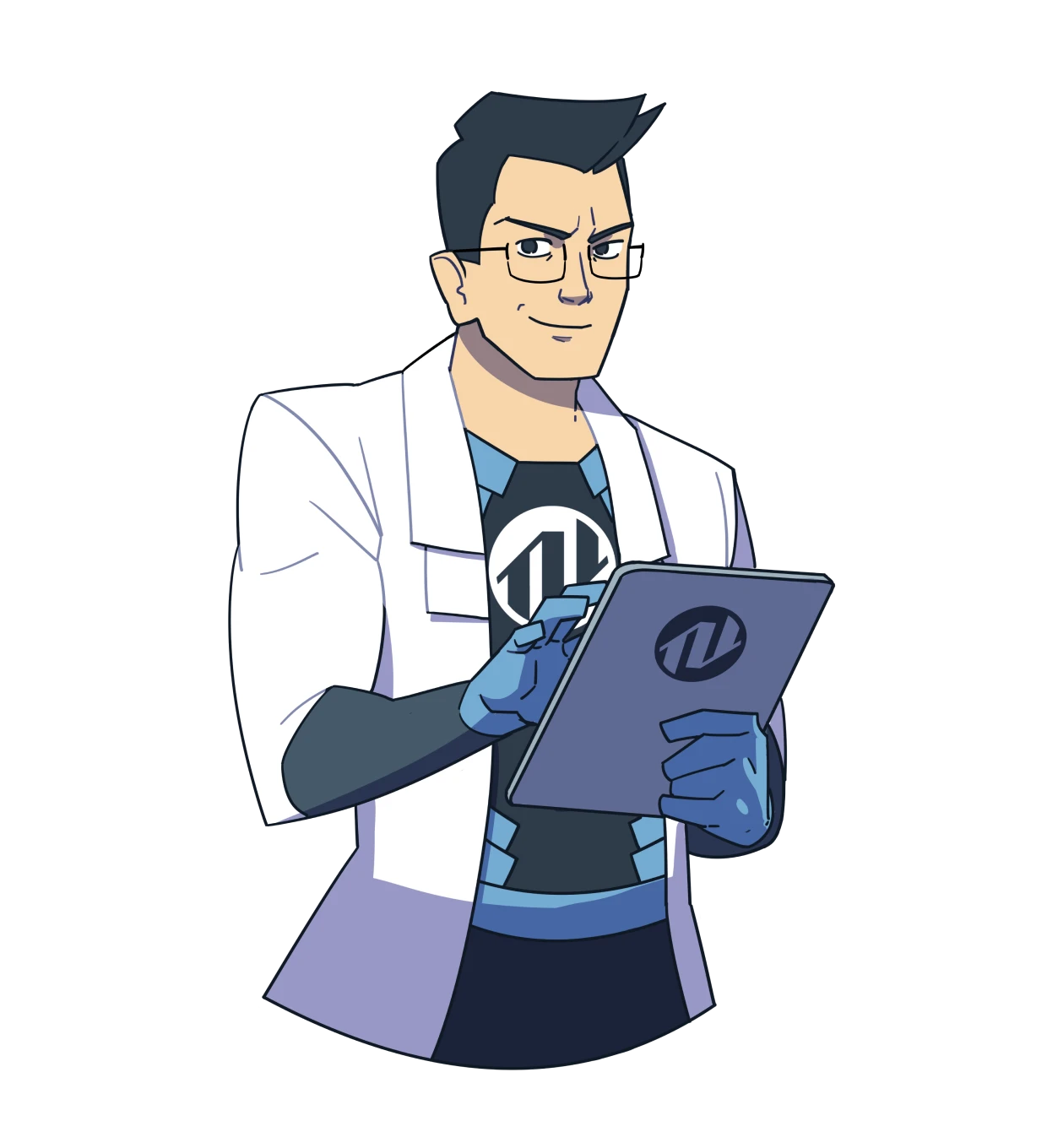
Many types of lasers are used in surgical applications, and the most common are:
- Erbium (Er:YAG) lasers
- Neodymium (Nd:YAG) lasers
- Holmium (Ho:YAG) lasers
- Thulium (Tm:YAG) lasers
- Excimer lasers
- Diode lasers
So why is it difficult for coaters?
- Absorption. The driver of laser damage must be minimised to ensure minimal loss and high LIDT.
- Laser-Induced Damage Threshold. Must be high to work with high-energy pulses.
- Deposition length. Mid-IR optics require long deposition processes due to their thickness, leading to higher costs of the final product.
- Difficulty of effective pumping and emission separation. The effectiveness stands solely on the performance of laser optics. And OPTOMAN is ready to optimise it to your specific laser requirements, ensuring the best possible outcome.
Features
- Low absorption. At some wavelengths and configurations, OPTOMAN managed to minimise the absorption to below <1 ppm.
- High LIDT. OPTOMAN thrives on achieving high LIDT and has reached values such as >168 J/cm2 @ 1064 nm, 9.8 ns 100 Hz, 223 µm.
- Long lifetime. At some wavelengths, over 10000h of a lifetime before the first downtime. At certain wavelengths, OPTOMAN also eliminated the color-change effect without influencing the catastrophic mode of laser damage.
- Thinner coatings. Our R&D team developed the capability of making relatively thin coatings for the Mid-IR thus significantly reducing coating time, which allows for cost-efficient and even more budget-friendly solutions.
Another important thing to mention is that water has absorption lines at 2 and 3 µm. Unfortunately, water vapor is prone to entering unwanted places, such as the pores in the coating, which in general leads to absorption-induced losses. However, the bulk-like density of coatings made with Ion-Beam Sputtering technology eliminates this problem, because there are no pores in the coating for the vapor to go in. This further proves that IBS is superior to other sputtering technologies.
OPTOMAN is also capable of manufacturing more complicated laser optics, such as wavelength separators and thin-film polarizers, even for the Mid-IR part of the spectrum, with expertise in handling different IR substrate materials.
Design variations
High reflectance example for Tm:YAG
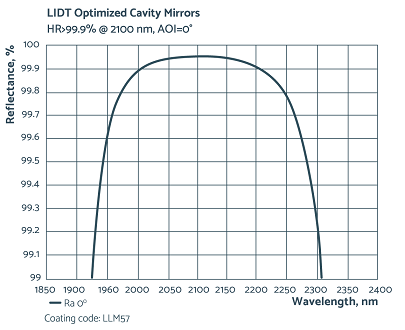
Partial reflectance example for Tm:YAG laser
.
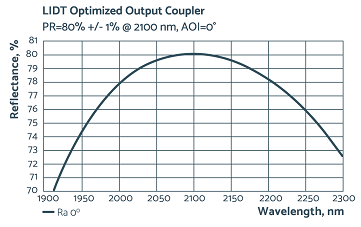
Anti-reflective example for Tm:YAG laser
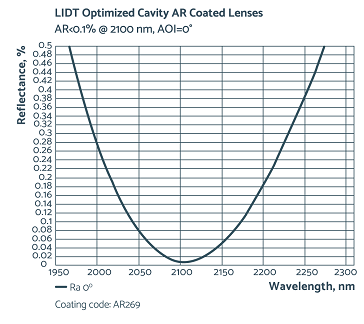
High reflectance example for Er:YAG laser
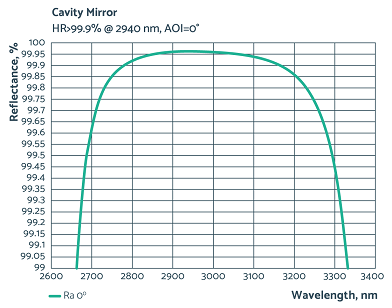
Partial reflectance examples for Er:YAG laser
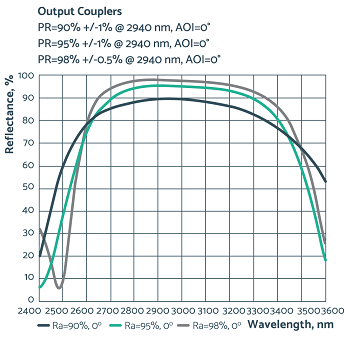
Partial reflectance examples for Er:YAG laser
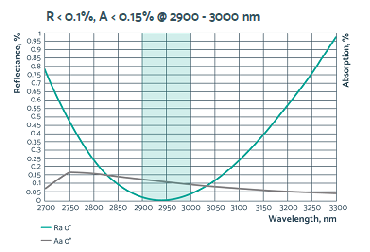
High reflectance example for Nd:YAG I and II harmonics
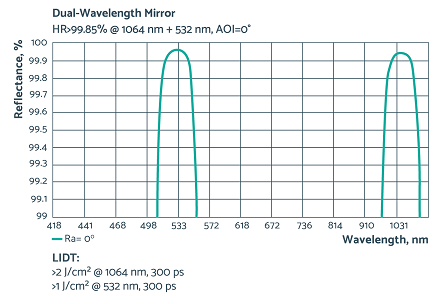
Cost efficient solutions
Recent developments at OPTOMAN destroy the myth that IBS coatings must be expensive. R&D team of OPTOMAN delved into coating material research and developed the capability of making relatively thin coatings for the Mid-IR region thus significantly reducing the main cost driver – time.
This means you don’t need to sacrifice spectral performance by choosing metal coatings or evaporation coating methods in order to remain within your target price.
Coating (IBS):
Ra >99.8% @ 2100 nm, AOI=45°
Coating (IBS):
Ra > 99% @ 2940 nm, AOI=45°
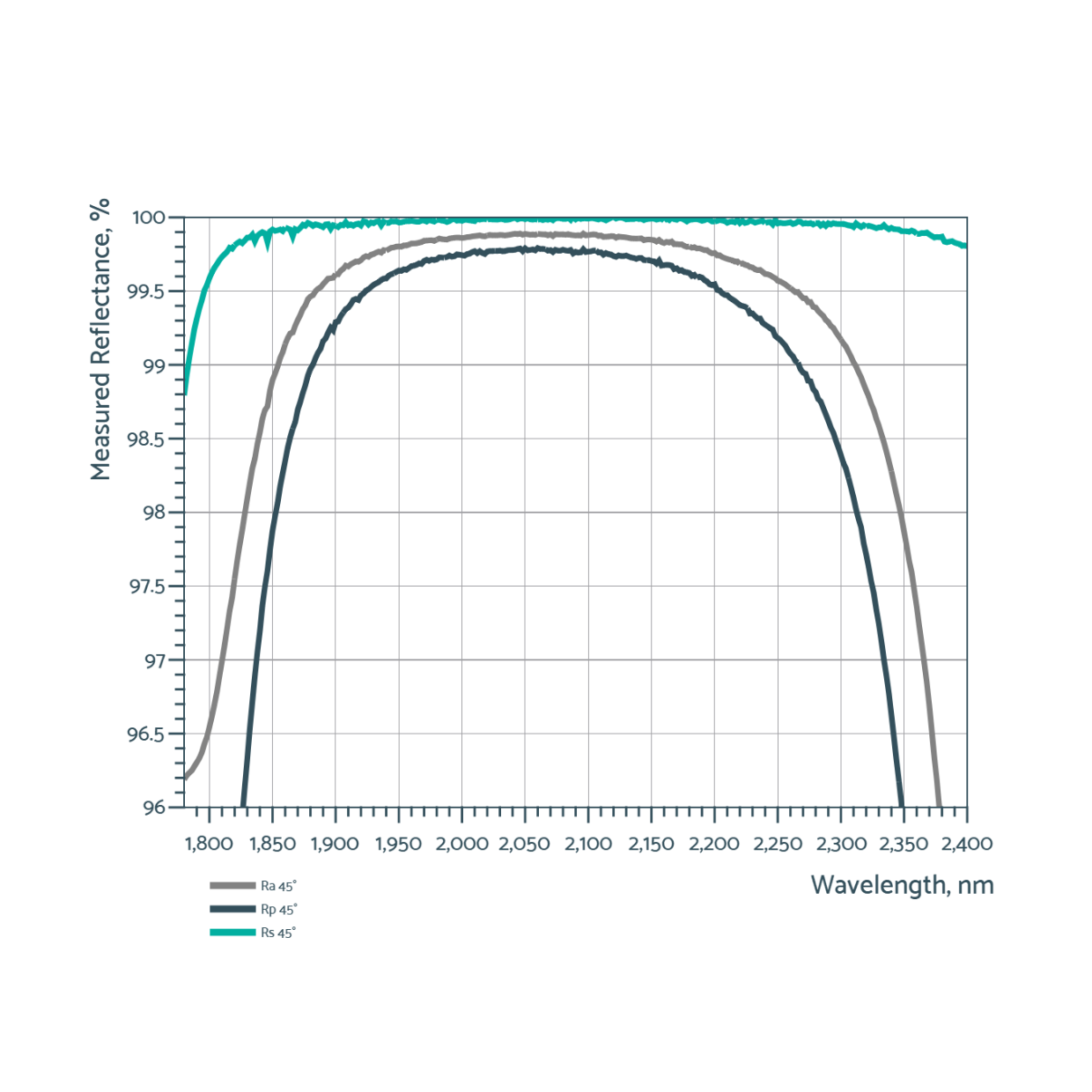
What about excimer lasers?
While the Mid-IR is crucial, excimer lasers, one of which (ArF laser) emits 193 nm deep-UV light, also play a big part in surgical applications. OPTOMAN has made the achievement of beating the market average – reaching R>98% @ 193 nm, AOI=45⁰ and doing it repeatable.
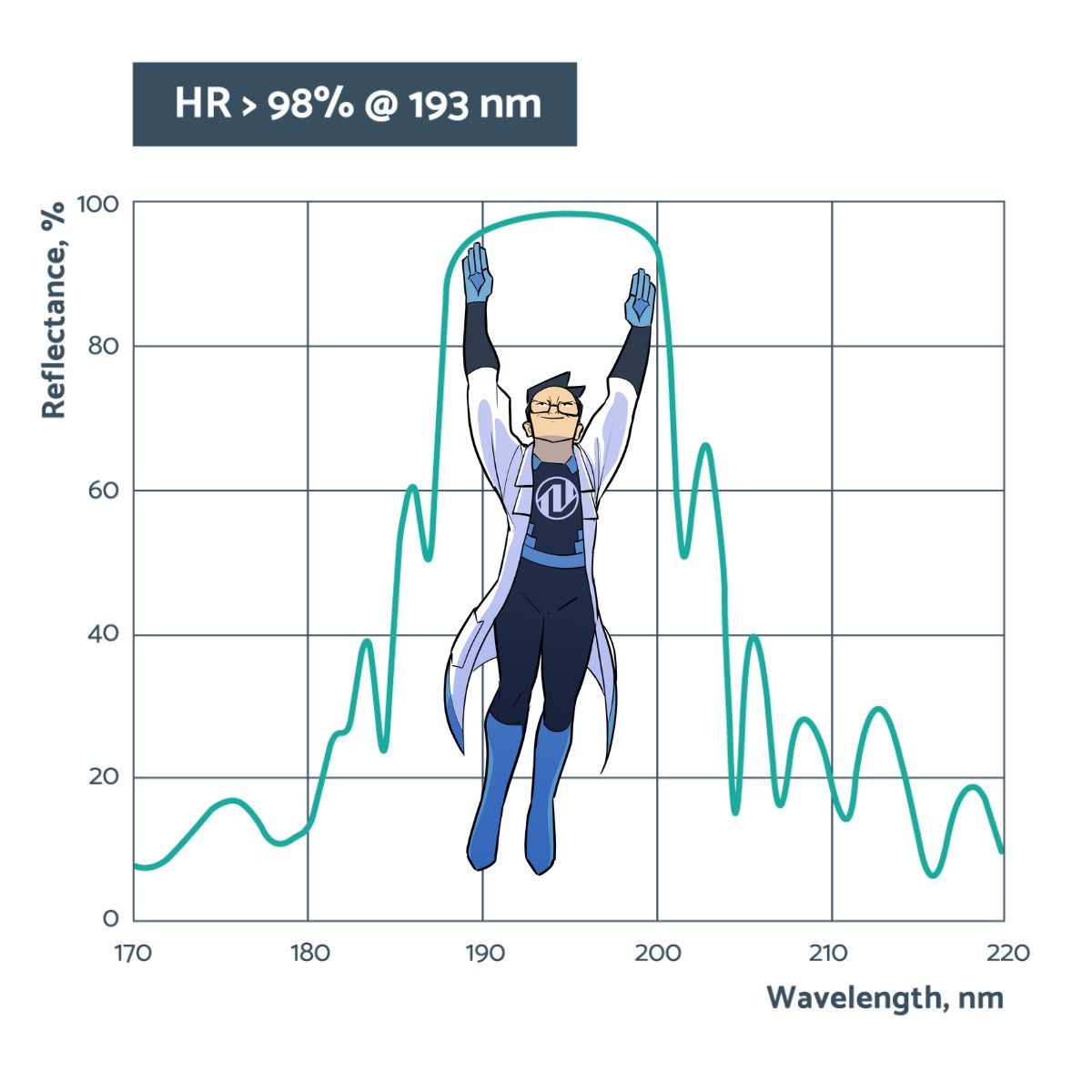
Many more custom variations of laser optics for surgical applications are available, even optical assemblies, such as light pipes. After all, the medical segment is our second largest market segment and in 2023 medical laser manufacturers generated 20% of OPTOMAN’s revenue.