Mid-IR Capabilities
Overview
With great [laser] power comes great responsibility [for coaters].
Laser optics for this region must feature high spectral performance and low absorption. Although scattering might not be a significant issue when speaking of Mid-IR optics due to the long wavelengths, absorption remains a serious concern, because it leads to reduced Laser-Induced Damage Threshold (LIDT).
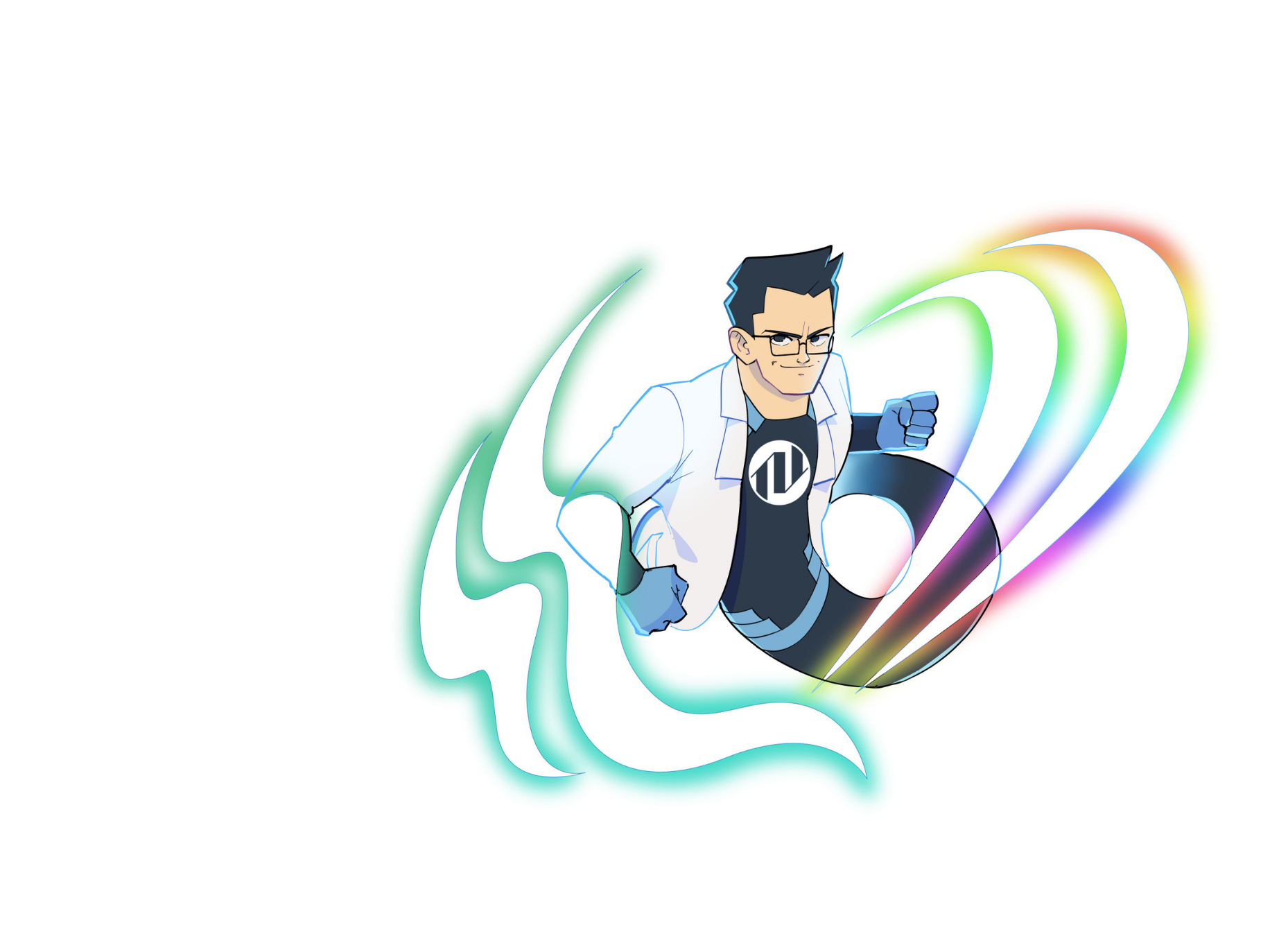
And here’s where OPTOMAN comes in. OPTOMAN concentrates solely on the most advanced sputtering technology – Ion-Beam Sputtering (IBS), which offers many great capabilities in depositing thin film coatings with great uniformity and bulk-like density.
Why is IBS more advantageous?
IBS solves key problems for Mid-IR coatings by:
- Improving coating density, ensuring long-term durability in harsh and dynamic environments.
- Minimising absorption losses, which helps optimise the output power of lasers.
- Improving LIDT and enabling operation at high-power levels.
So what are the challenges related to using IBS for Mid-IR coatings?
- Film Stress. It is true that IBS coatings due to high density have higher stress values that can lead to coating cracking or peeling. At OPTOMAN, by introducing specific pre- and post- coating processes, we were able to reduce the stress which leads to fewer of the aforementioned problems.
- Adhesion issues. Substrate material properties as well as differences in thermal expansion coefficients typically cause adhesion issues for IBS coatings. OPTOMAN was no exception, but R&D department found the way to make high repeatability optics for Mid-IR.
- High cost. Coatings for Mid-IR spectral region are usually quite thick, which sometimes motivates to avoid IBS coatings and sacrifice some of the performance for the better price provided by alternative coating technologies or metal coatings. However, OPTOMAN now offers two alternatives that addresses the cost drivers:
1) Scale. OPTOMAN has one of the largest IBS coating chambers in the World enabling to reduce the cost per piece significantly.
2) Coating thickness. Recent R&D achievement enables OPTOMAN to offer relatively thin coatings that perform like you would expect from IBS coatings but with a significantly reduced price. This technology is suitable for <100 GW/cm² laser power levels and is a perfect choice for laser communication applications, environmental monitoring, sensing and imaging. By this innovation, you can remain at your target price, but improve your laser system performance by advanced IBS coatings.
Due to these challenges, it is not common to manufacture Mid-IR laser optics with IBS technology. However, OPTOMAN has overcome and solved these problems and confidently believes that using IBS is advantageous for the reasons mentioned above. OPTOMAN can make all types of coatings – anti-reflective, mirrors, GTI mirrors, polarizers, partial reflectors, dichroic mirrors, etc. up to 5000nm.
One more important thing… substrates
- IR Fused Silica (0.3 – 3.5 µm): One of the most commonly used substrates in this spectral region. In IR-grade fused silica, it is essential to have a low content of hydroxyl (OH), with content values typically below 10 ppm. Substantial absorption bands related to hydroxyl content are around 2.2 μm and 2.7 μm wavelength, but there are also overtone bands e.g. in the 1.4 μm region, which are relevant for the 1.5 μm telecommunications wavelength band.
- CaF2 (0.2 – 9 µm): It possesses excellent IR spectral performance, high laser durability, low-stress birefringence, and high refractive index homogeneity. It is one of the most versatile and popular substrates for Mid-IR spectral region.
- Sapphire (0.3 – 5 µm): Most suitable for high power applications. Sapphire has many advantages, such as extreme surface hardness and scratch resistance, wide optical transmission band from UV to Mid IR (190 nm – 5000 nm), high melt temperature and chemical inertness. A high grade of sapphire would have little or no light scatter or lattice distortion and be used mainly for the most demanding optical applications.
- Germanium (2 – 14 µm): It has good thermal conductivity and is very hard due to having the same crystal structure as diamond. It has low dispersion making it suitable for Mid-IR ultrafast lasers, however limited to low power lasers due to severe refractive index dependence on temperature and high nonlinear index. The most common application is imaging.
- Silicon (2 – 5 µm): It has slightly lower refractive index than Germanium and is very hard and stable over different temperatures making it suitable for extreme environments.
- YAG (0.3 – 4 µm): A viable choice for high-power applications. It has low internal stress, high hardness, chemical and heat resistance. What is most interesting about this substrate is its lack of birefringence making it quite unique and applicable for high-energy/high-power laser systems.
- ZnSe (Zinc Selenide) (0.6 – 21 µm): It has a broad transmission spectral range, low absorption, low scattering, and a high damage threshold.
All in all – knowing about various substrates and their advantages/disadvantages is of great importance. And OPTOMAN knows how to prepare various substrates for coating runs and finally achieve laser optics with high adhesion, reliability, and repeatability.
But what tech note without examples? Let’s move on and see what we’re actually capable of.
Part I: Ultrafast Mid-IR Optics
Coating (IBS):
HRp>99.8% @ 1900-2700 nm + HT>97% @ 1550 nm, AOI=0-5°, |GDDr | <100 fs² @ 1900-2700 nm
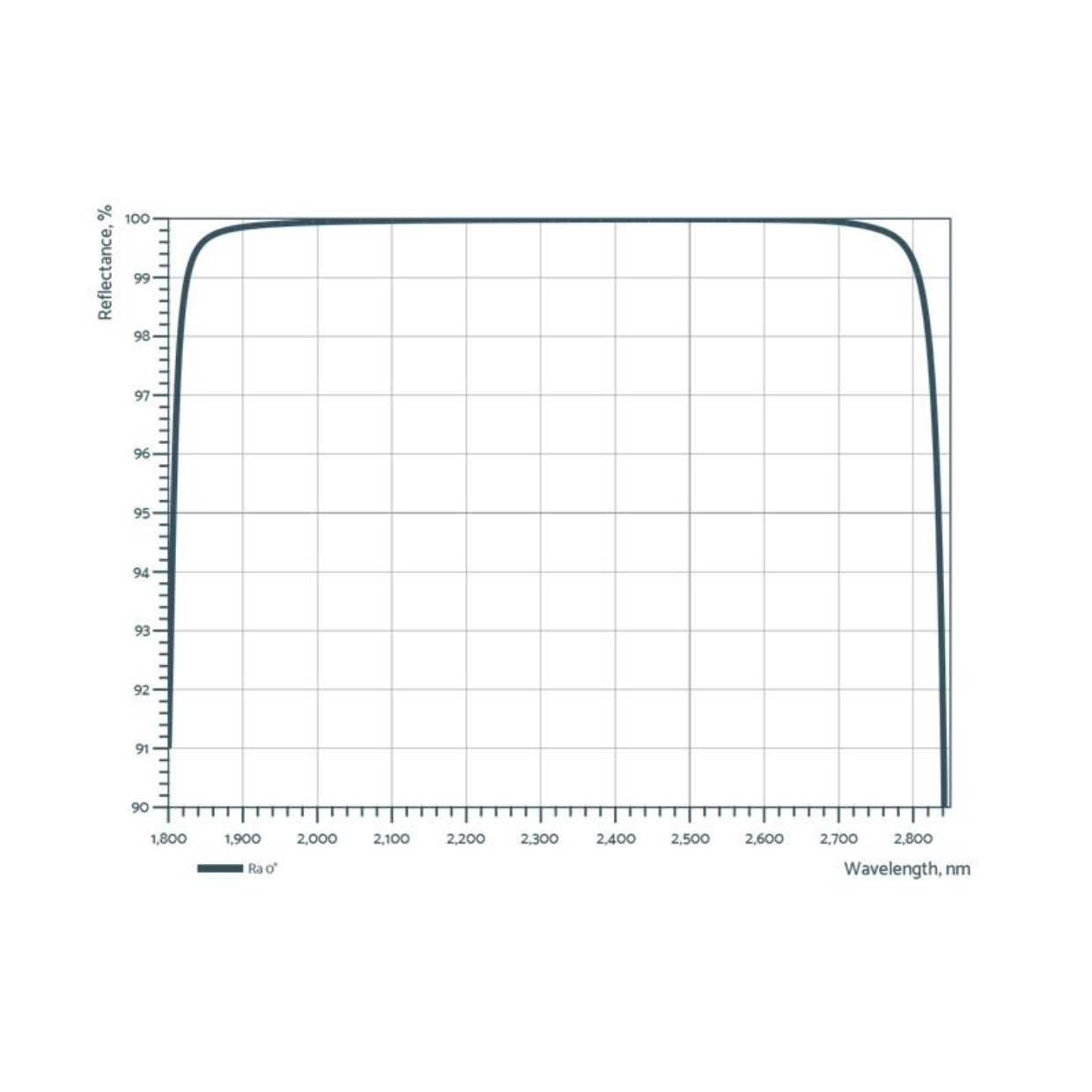
Transmission spectrum of the same coating
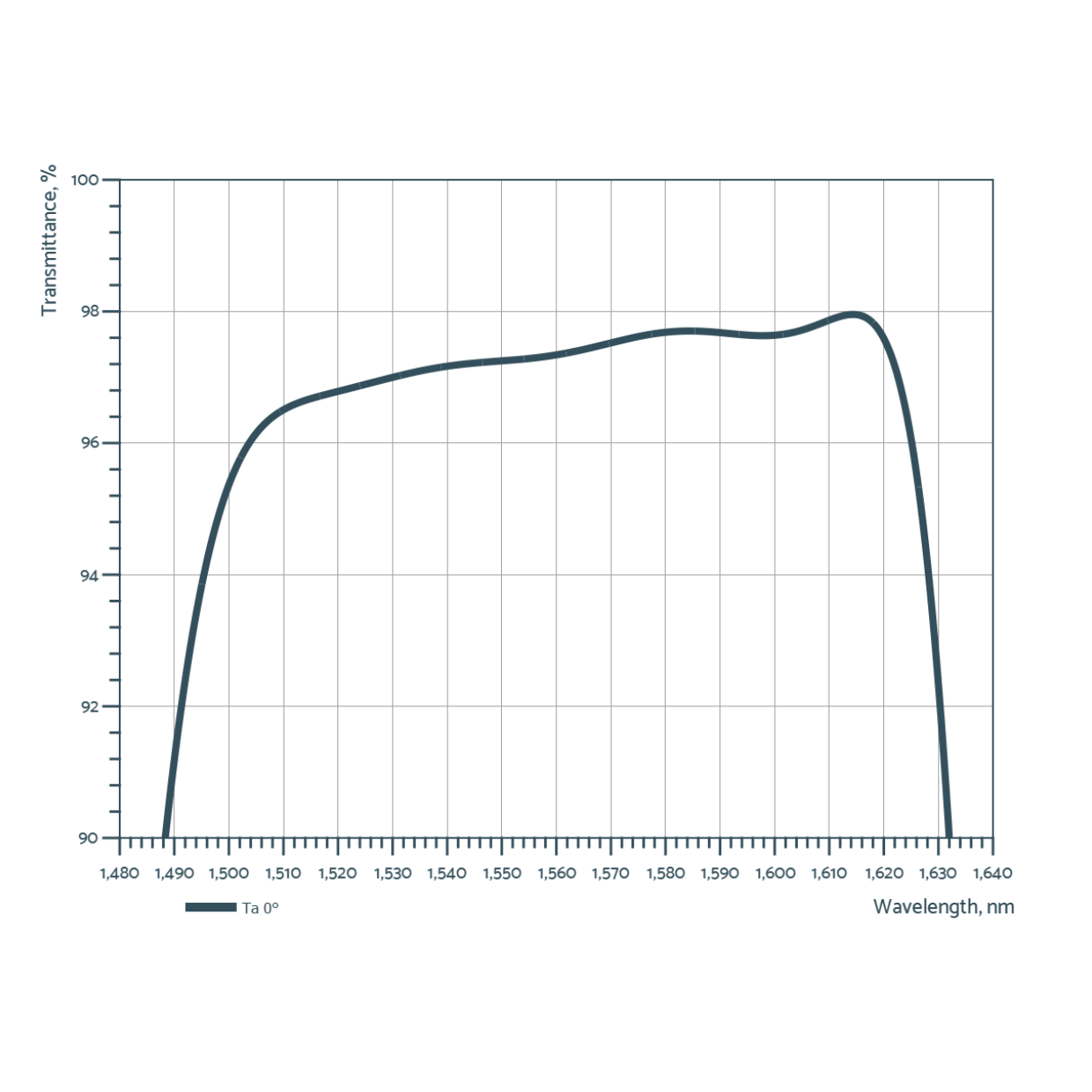
In need of low and spectrally uniform GDD?
Not a problem!
|GDDr | <100 fs² @ 1900-2700 nm
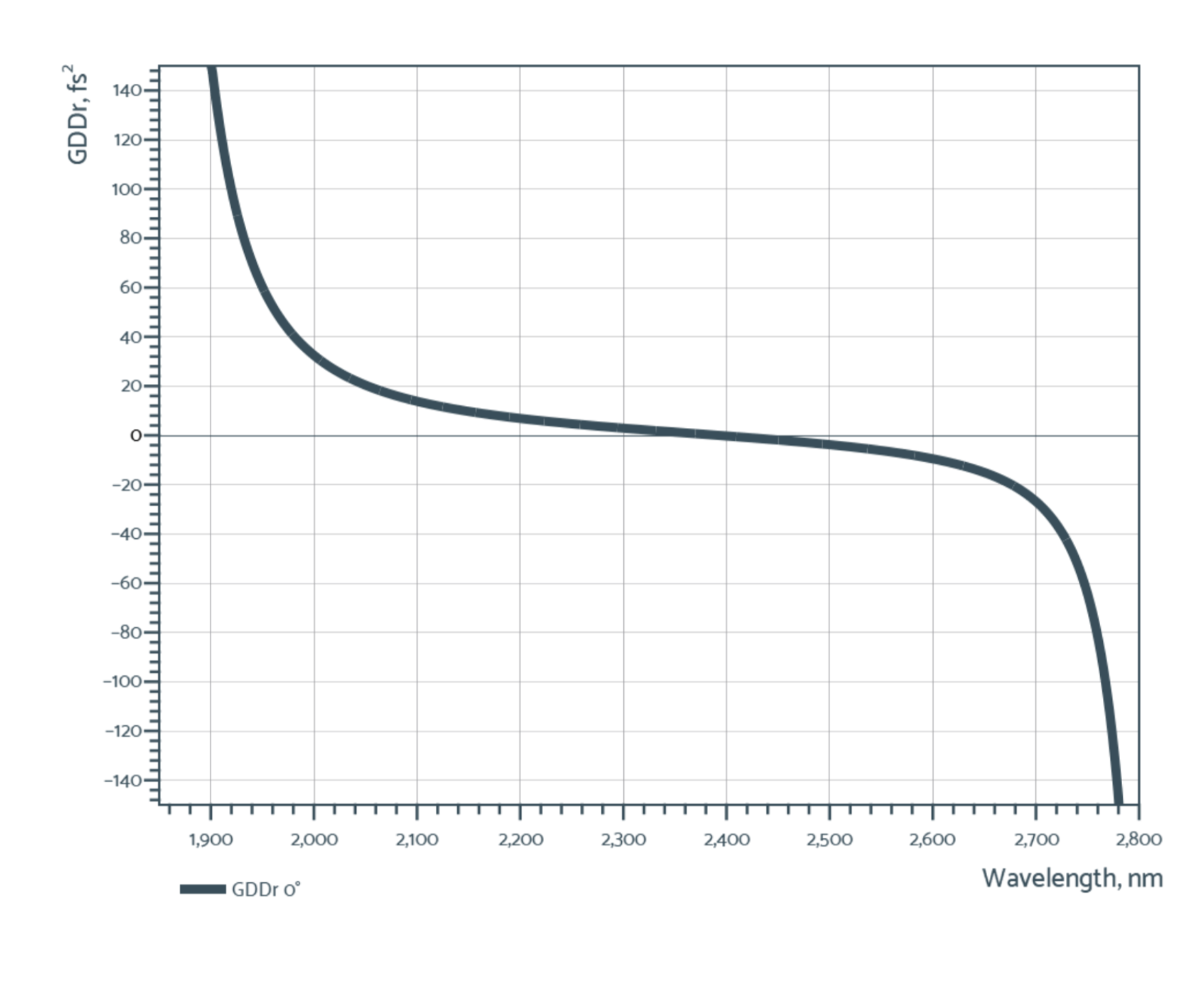
Oh sorry, you meant Highly Dispersive Mirrors?
Not a problem as well!
OPTOMAN is one of the first companies worldwide to offer Highly Dispersive and broadband mirrors made for Mid-IR spectral range with IBS technology, which can be used as the straightforward means to compensate dispersion and compress ultrafast mid-IR laser pulses.
To the right you can see a theoretical reflectance and GDD curves for a broadband Mid-IR mirror.
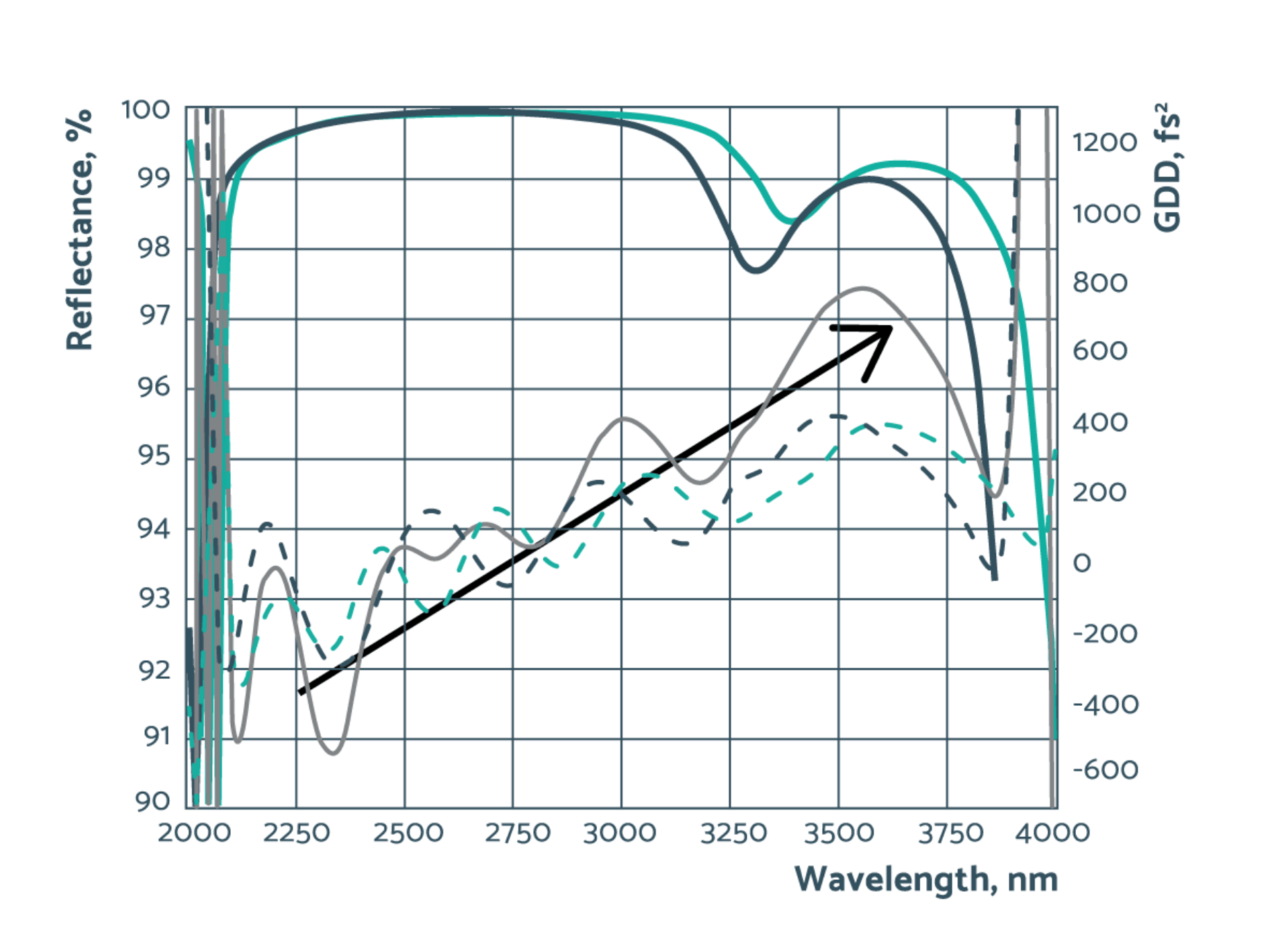
Usually, the Highly Dispersive Mid-IR technology relies on combining transmissive materials with opposite signs of group velocity dispersion (GVD) (e.g. semiconductors and dielectrics), however strong absorption bands limit the transmittance in this spectral region, which limits the ability to adjust the chirp. Broadband dispersive mirrors, on the other hand, can reduce, or even eliminate the need to use such combinations to compensate dispersion and finally recompress broadband pulses close to Fourier limit duration in the sub-2 cycles regime. Which in the end allows shorter pulse durations and higher peak intensities.
Part II: Optics for Er:YAG lasers
One of the most common lasers in this spectral region is the Er:YAG laser. It emits light that strongly corresponds to absorption bands in water, thus it is well suitable for medical applications. OPTOMAN is capable of manufacturing long lifetime and high LIDT laser optics at 2940 nm with high confidence because of the procedures which lead to almost full reduction of OH group absorption inside the coating.
To the right, you can see a Sapphire AR/AR coated window example.
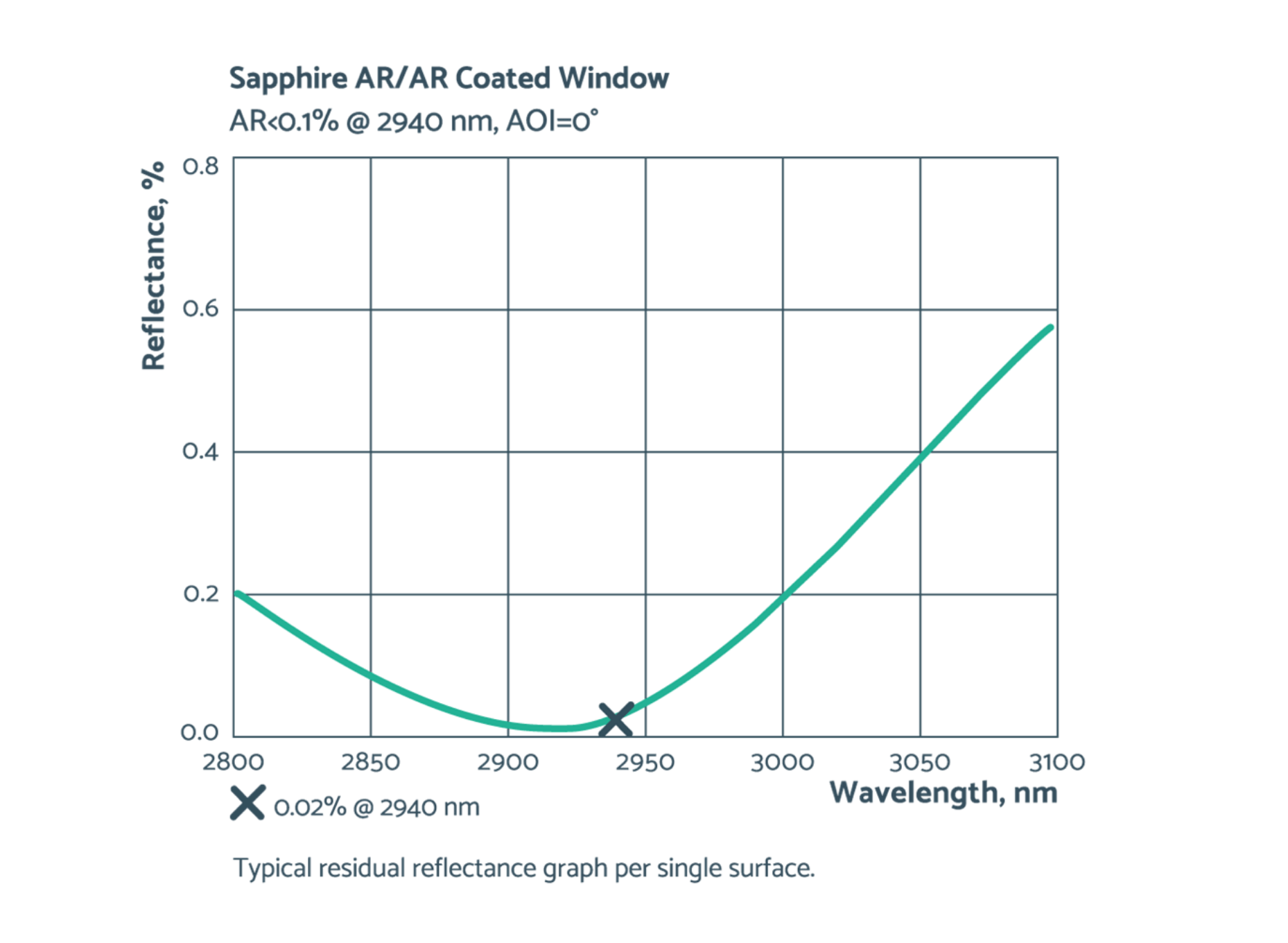
Coating absorption <0,2% @ 2940 nm (per surface).
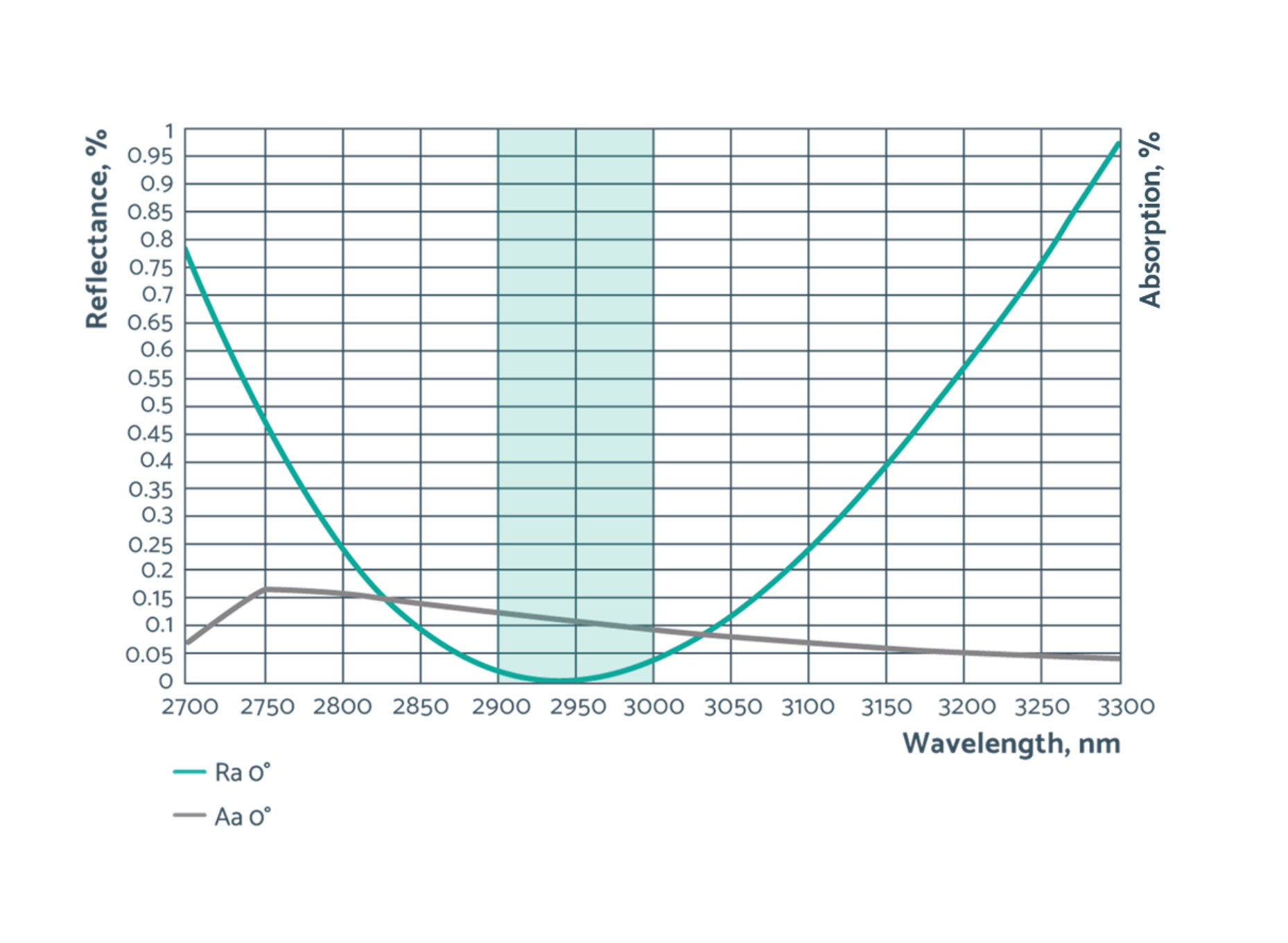
Part III: Cost efficient Mid-IR optics
Any examples for the cost effective laser optics? Plenty!
HR>99.9% @ 1900-3000 nm, AOI=0°
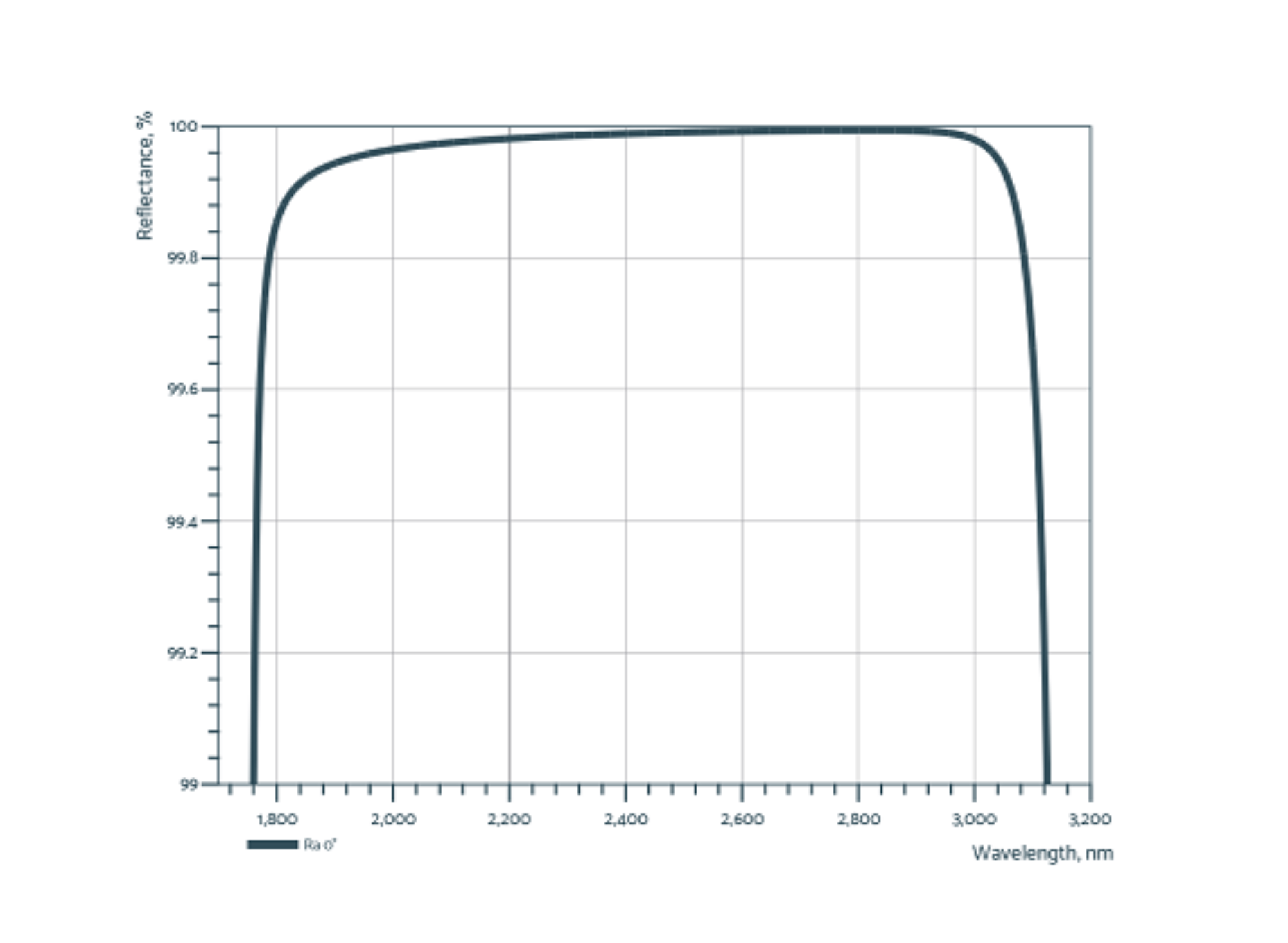
AR>0.1% @ 1900-3000 nm, AOI=0°
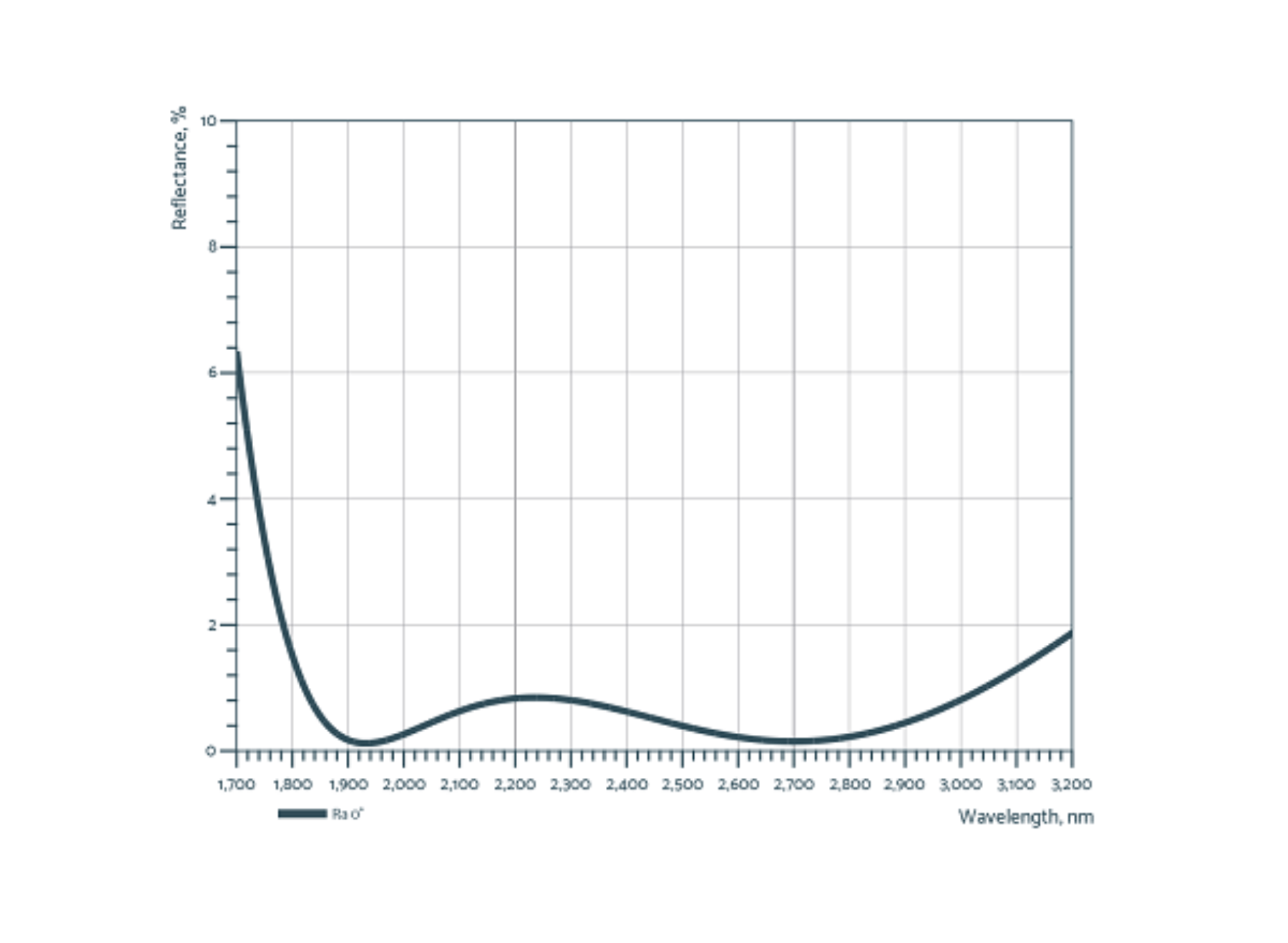
PR=80% @ 1900-3000 nm, AOI=0°
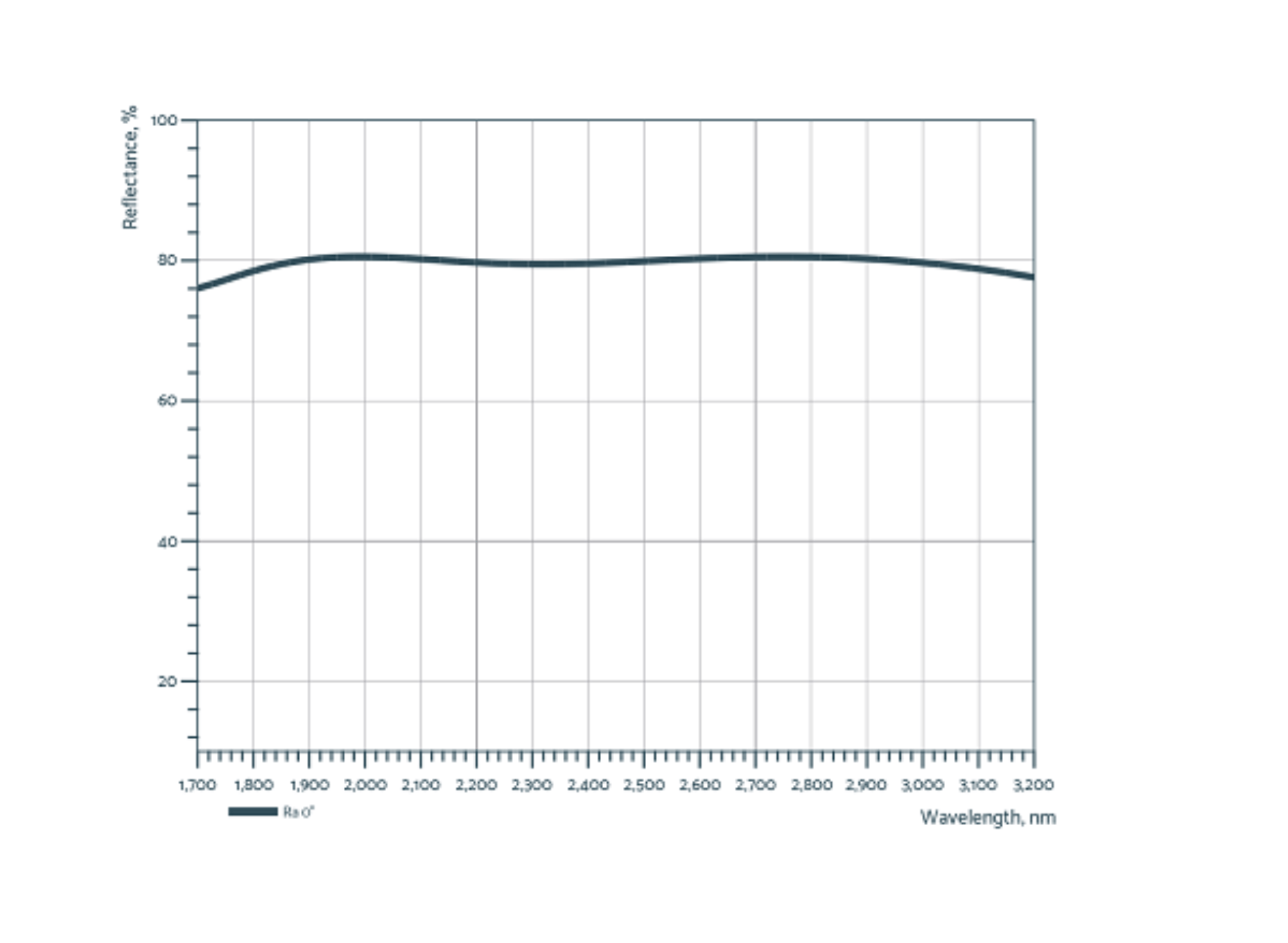
PR=50% @ 1900-3000 nm, AOI=0°
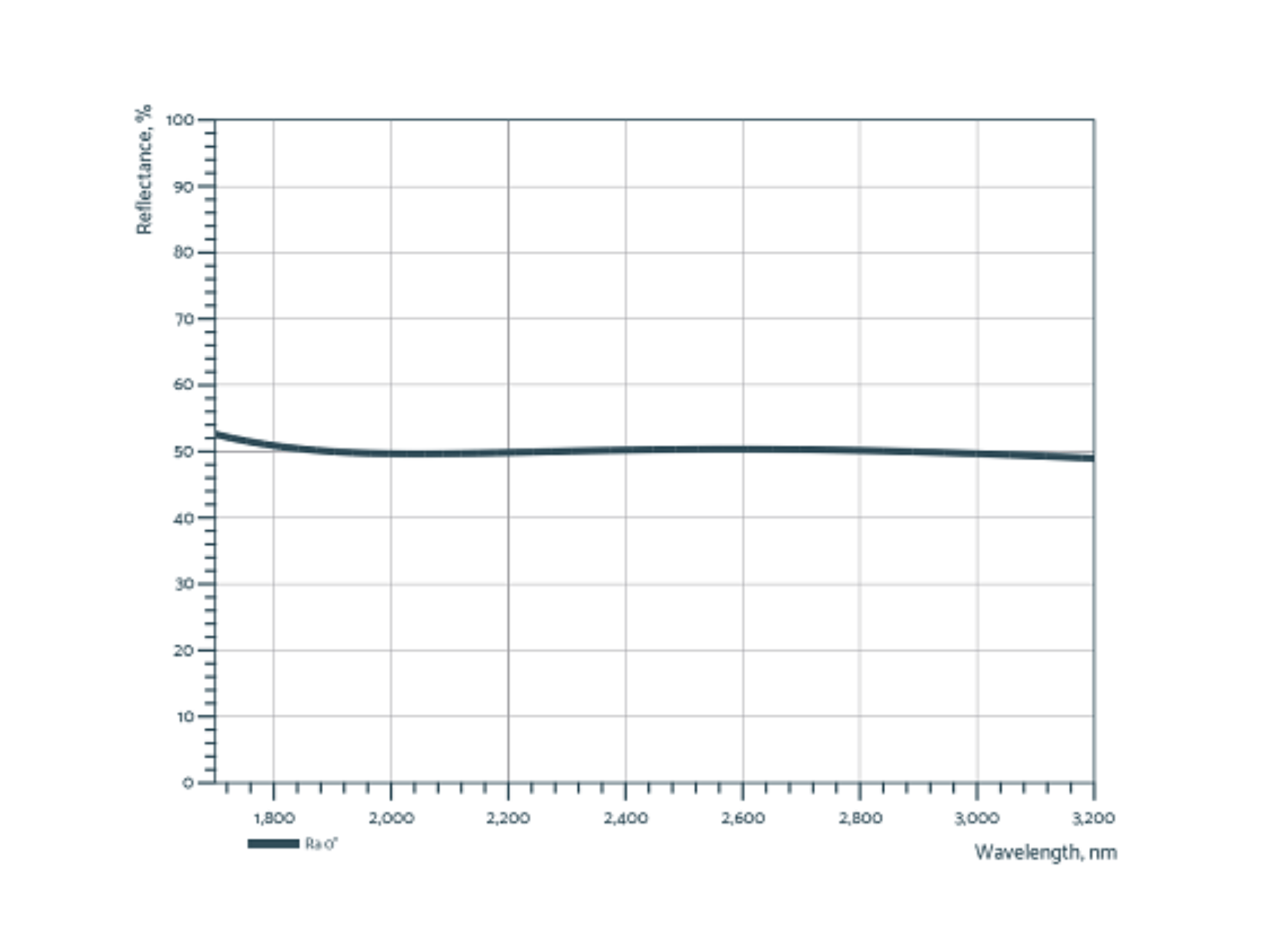
HR>99.9% @ 3400-5300 nm, AOI=0°
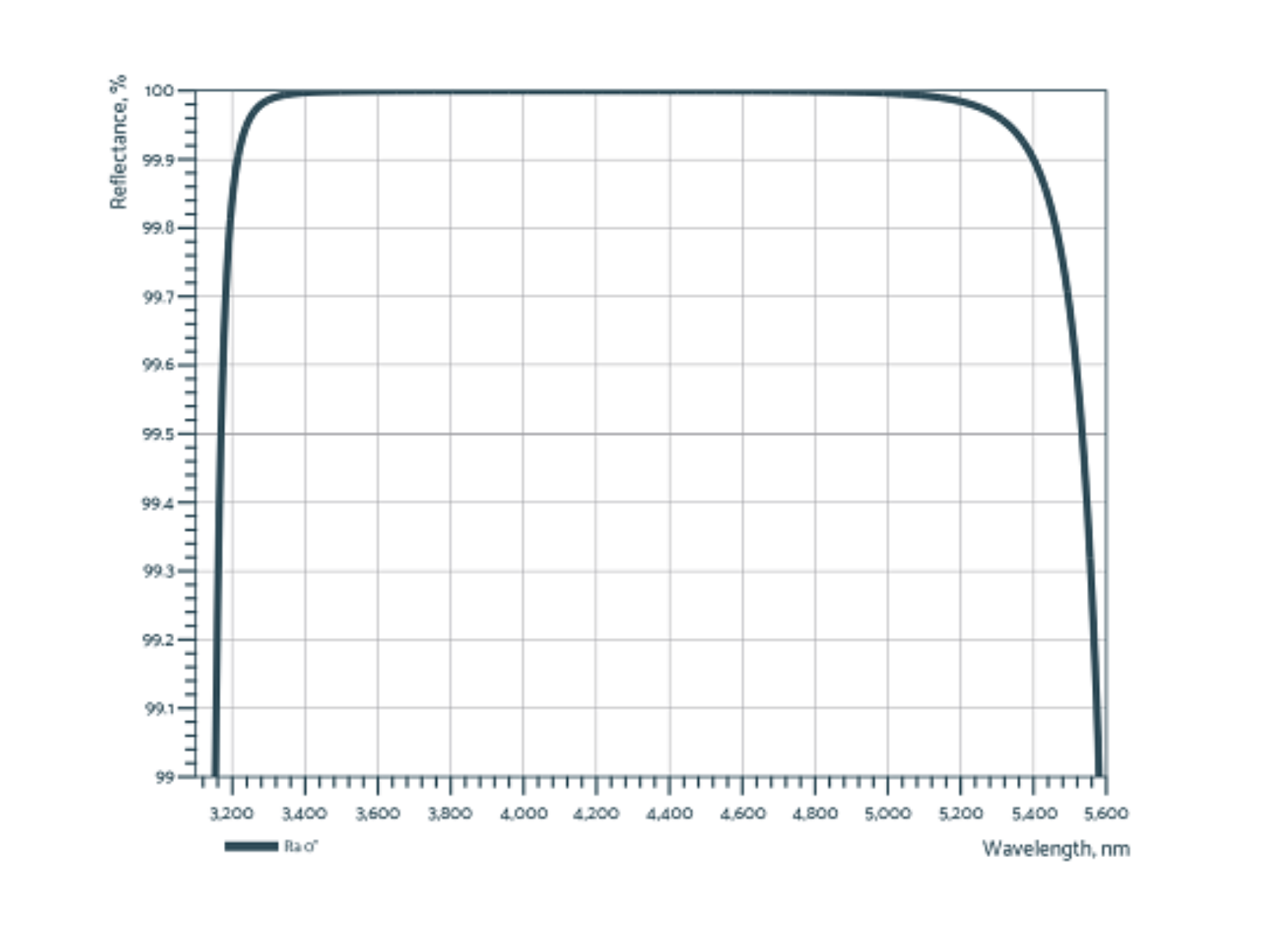
Measured reflectance at AOI=45°
Our R&D team developed the capability of making relatively thin coatings for the Mid-IR thus significantly reducing coating time.
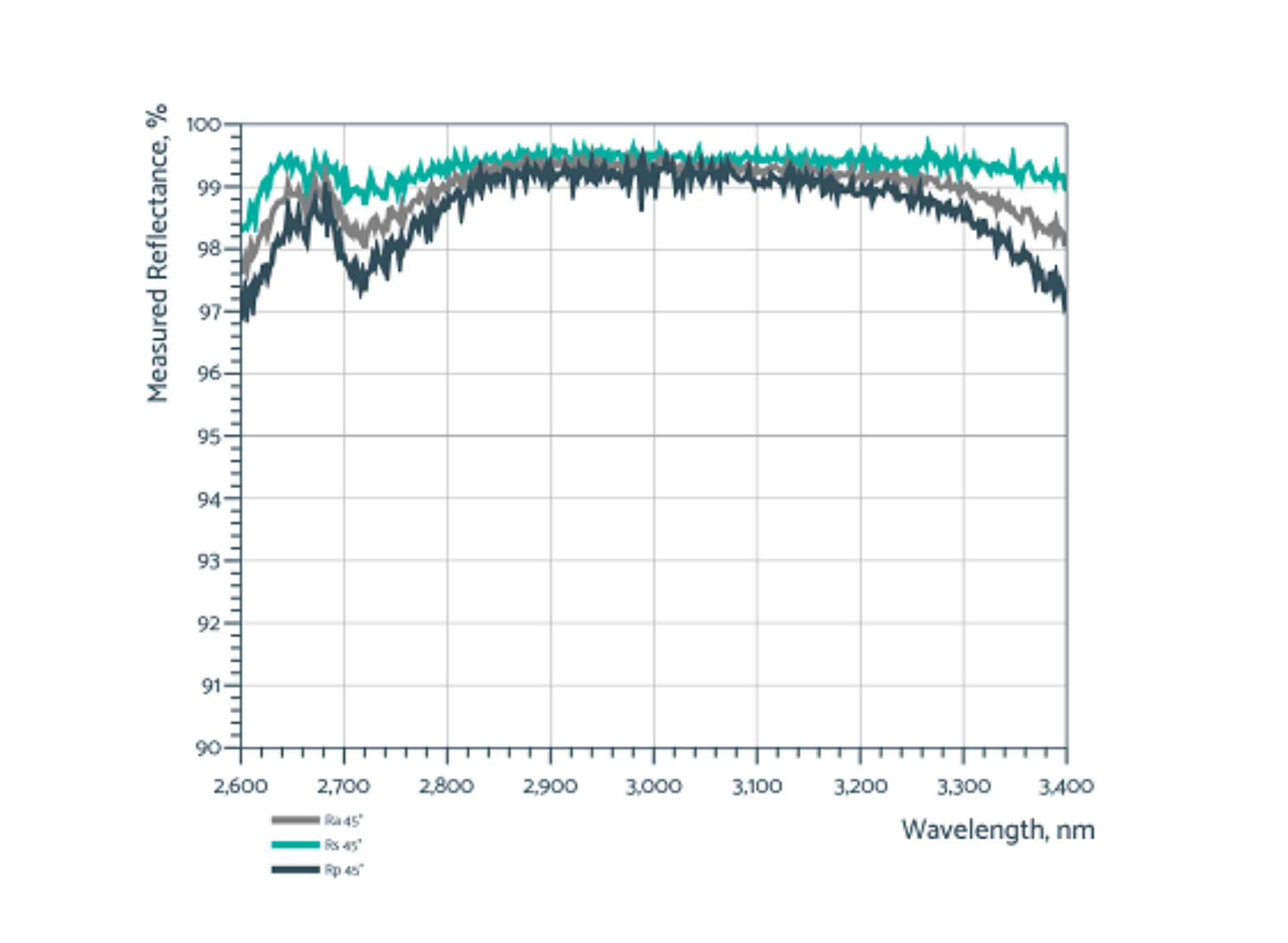